Aero Contractors expands facility, targets one-stop MRO
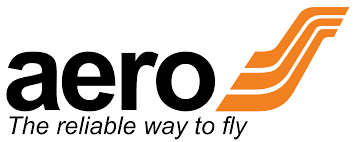
Aero Contractors Airline has commenced the expansion of its maintenance, repair and overhaul facility with the dream of transforming it into a one-stop maintenance hub for Western and Central Africa while also enhancing its heavy maintenance visits capability.
The managing director of the airline, Capt Ado Sanusi, made this known shortly after signing a pact with the Nigerian Safety Investigation Bureau for industry-led safety training, knowledge exchange, and human capital development to further strengthen safety in the industry.
Sanusi said the MRO is currently undergoing renovation and hangar expansion, which he said should be completed within 90 days.
He added that the company is gradually retooling to enhance its maintenance capabilities.
Speaking on the scope of maintenance, Sanusi disclosed that the MRO currently works on several aircraft types, including Boeing 737 NGs, Airbus A320s, CRJs, and Embraer 145s.
The company is investing heavily in infrastructure improvements, such as raising the hangar roof, redoing the flooring, enhancing electrical systems, and upgrading lighting.
“We are also acquiring new tools and upgrading the hangar to the next level. Our workshop has been modernised and is undergoing expansion to cater for both older and new-generation aircraft,” Sanusi stated.
In a statement, Aero Contractors announced securing line maintenance contracts with operators of Boeing 737 MAX and 787 Dreamliners, with the MRO aiming to support customers flying these advanced aircraft.
“We are building the capability for the CRJ and intend to handle engine maintenance, auxiliary power unit overhauls, landing gear repairs, and component servicing. We can perform up to D-checks on Boeing 737 Classics and Dash 8 aircraft. Our objective is to be a one-stop maintenance hub in Western and Central Africa, and we are making steady progress toward that vision,” Sanusi concluded.
Sanusi further clarified the distinction between scheduled checks and heavy maintenance visits, saying, “Scheduled checks are categorised into A, B, C, and D checks. The A and B checks are typically line maintenance tasks performed at regular intervals based on flight hours or calendar time. The B check, although part of line maintenance, can sometimes be conducted at a base facility.
“The C check, performed at a base maintenance facility, is more extensive and involves thorough inspections and system checks. It is divided into subcategories such as C1, C2, up to C6, culminating in the D check, which is the most comprehensive and invasive inspection. These checks are both hours and calendar-driven, ensuring the aircraft remains airworthy and compliant with regulatory requirements.
“On the other hand, Heavy Maintenance Visit operates under the Maintenance Steering Group programme. Unlike traditional checks that are calendar-driven, HMV focuses on component reliability and performance. This approach is based on real-time data and the operational history of aircraft components. By assessing the hours each component has logged, maintenance actions are scheduled based on actual wear and performance rather than fixed calendar timelines.”
Sanusi further said HMV methodology is particularly applicable to newer generation aircraft, where manufacturers have gained confidence in the reliability of the components over time, saying, “This approach allows for more efficient maintenance planning, reduces unnecessary downtime, and enhances the overall safety and longevity of the aircraft.”